5. Fräsen der O-Ring Nuten und Bohren der Verschraubungen
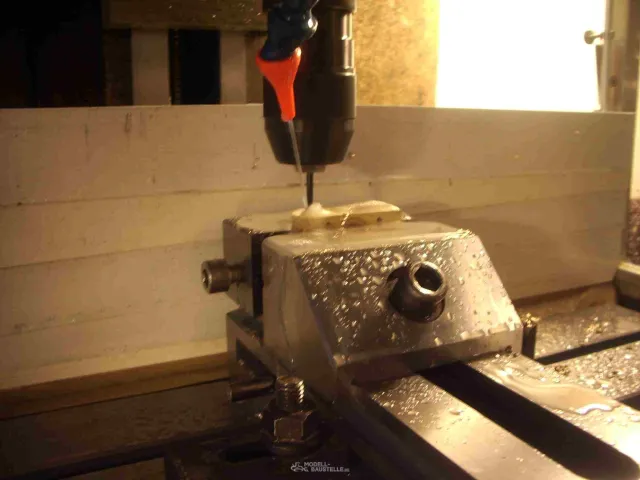
Deckel:
1. Fräsen der äusseren Geometrie
2. Gleitführungs- und Nutringtasche drehen/ fräsen
Es gibt 2 Möglichkeiten zur Herstellung. Wichtig ist, alles in einer Aufspannung zu bearbeiten, da die Wellendurchführung und die Gleitführung des Drehschiebers konzentrisch zueinender sein müssen. Ausserdem müssen die Gleitflächen der Drehschiebers absolut zylindrisch sein.
Drehbank:
Spannen in einer Planscheibe. Ausrichten mit Messuhr auf "Rundlauf" der Seitenflächen (Rundlauf mit 10µm Uhr und Messweg 10mm)
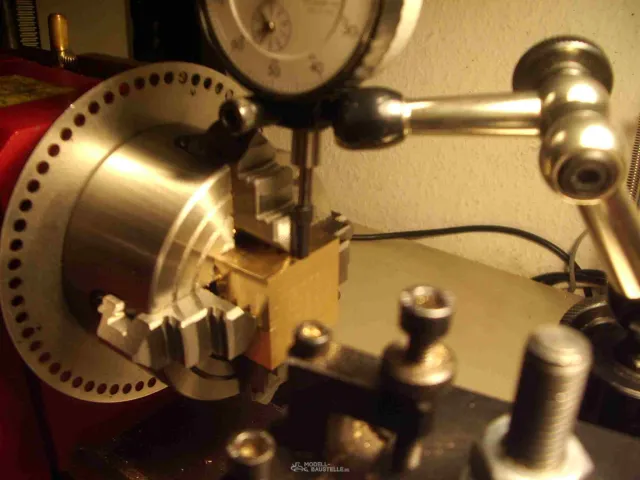
Plandrehen der Vorderseite.
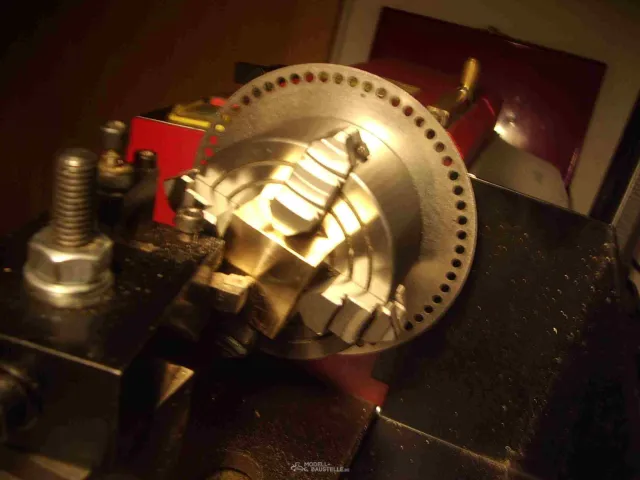
Taschen ausdrehen,auch die Wellenführung, und dann mit einer Reibahle aufreiben. Nur etwa 2/3 der Schneidlänge der Reibahle benutzen. (möglichst enge Toleranz) Mit H7 Passtift probieren ob sie der Stft leicht durchstecken läßt, ansonsten nachreiben.
Bohren der 4 Befestigungslöcher auf der Fräsmaschine
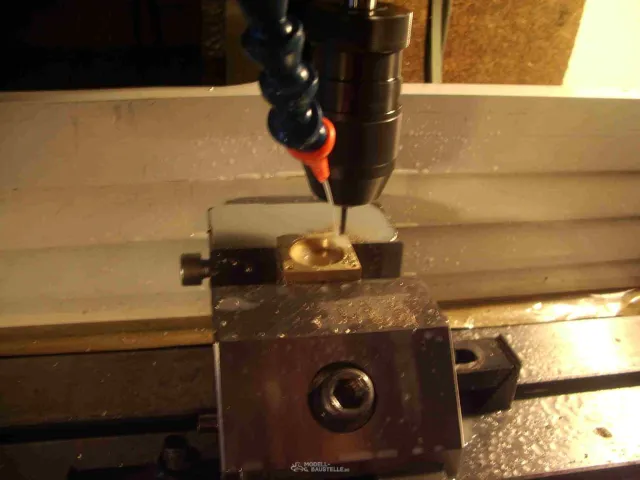
Fräsmaschine:
Planfräsen der Oberseite. Ausfräsen der Taschen, auch der Wellenbohrung. Schlichtgänge mit wenig Materialabtrag am Ende der Bearbeitung, sowie Benutzung eines scharfen Schlichtfräser d=8mm für das Fräsen des "Drehschiebergleitlagers"
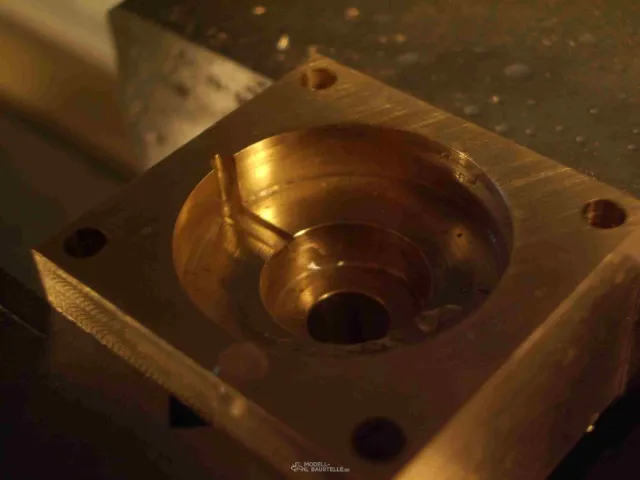
Aufreiben der Wellenführung und Bohren der 4 Befestigungslöcher wie oben beschrieben.